Navigating the Digitalisation Journey in the Biopharmaceutical Industry
Exploring the shift towards digitalisation in bioprocessing, from AI and cloud-based systems to overcoming challenges like regulatory hurdles, cost, and standardisation, while driving efficiency, compliance, and collaboration in bioprocessing.
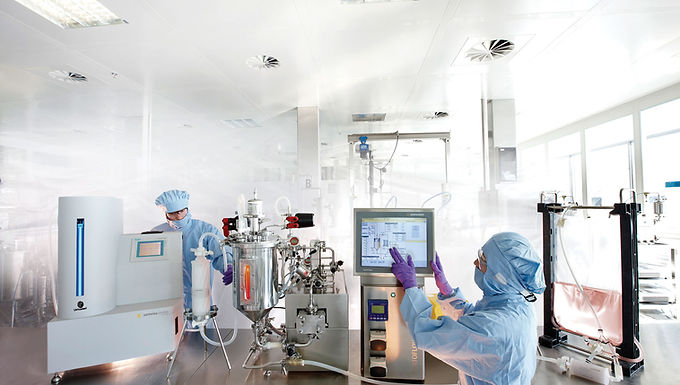
The bioprocessing industry, which typically involves the use of living organisms, cells, or their components to produce valuable products, has traditionally been slower than other sectors in adopting digitalisation. This slow adoption is often due to long-term reliance on manual processes, strict regulatory requirements, and resistance to change. However, digital technologies have been gradually transforming bioprocessing, enhancing efficiency, data management, and process optimisation over recent years.
Current adoption
A recent event held in 2024 hosted by partnerships between University College London and Accenture Innovation called "Reimagining the Future of Biopharma Digitalization”, gathered key stakeholders from across the biopharmaceutical sector, including academics, manufacturers, vendors, consultants, and policymakers. The findings from participants in this event highlighted that 46% of respondents are currently using a hybrid system combining digital and paper-based records, with partial data lakes and process analytical technologies (PAT) in development. This suggests that while digitalisation is progressing, more than half of bioprocessing organisations still rely on traditional record-keeping methods. Additionally, 32% of participants from the survey carried out reported primarily using paper records supplemented by an online data-management system that lacked PAT. This reflects the transitional phase many companies are in, where digital tools are being introduced but not yet fully integrated.
The push toward digitalisation has been largely driven by several factors including cost efficiency, operational flexibility, and process optimisation. Companies are leveraging digital tools to streamline workflows, reduce waste, and improve manufacturing efficiency. For example, AI and machine learning allow for predictive modelling that can optimise bioprocesses and find anomalies in real-time. One of the first steps towards fully incorporating digitalisation is the removal of paper-based records and replacing them with digital batch records and automated data capture systems. This shift helps reduce manual data transfers, while minimising errors and enhancing productivity. By adopting Electronic Lab Notebooks (ELNs) and Manufacturing Execution Systems (MES) over traditional paper-based systems, there will be improved traceability and streamlined manufacturing.
Many mid-to-large-sized companies in the industry began digitalising batch records by mid-2000s, significantly reducing paper records on manufacturing floors. However, legacy paper-based systems persist in some areas due to organic growth and prioritisation of investment. Process automation and the integration of data analytics are now expected across biomanufacturing sites, enabling companies to gain better process insights and control. Interestingly, the COVID-19 pandemic served as a major catalyst for digital adoption. The urgent need to develop and manufacture vaccines led to collaboration between biopharmaceutical companies and regulatory agencies, which accelerated the implementation of digital technologies to improve production efficiency and regulatory compliance. In contrast, smaller companies have taken a more targeted approach, adopting digital capabilities that address immediate operational, and compliance needs to help provide competitive advantages. For example, contract service providers in particular, leverage digitalisation strategies to enhance flexibility, scalability, and collaboration with customers and regulators.
A compelling example of digitalisation in the bioprocessing industry involves the collaboration between Cytvia and Biogen. Here, they wanted to identify gaps and potential risks that were missed during processes. By combining process data from the manufacturer with detailed raw material data from the supplier, they applied AI-driven models to predict key attributes and improve control and risk mitigation. They demonstrated how digitalisation can drive process improvements, enhance quality assurance, and reduce batch failures by leveraging real-time and retrospective data analysis. Furthermore, they showcased the importance of long-term partnerships and trust between parties for successful digital adoption.
Barriers to adopting digitalisation
As the industry continues this digital transition, the integration of cloud-based systems, AI-driven analytics, and automation is expected to drive further advancements. While efforts are being made to promote the adoption of digitalisation in the industry, there are several challenges that persist. Firstly, many professionals prefer reliance on traditional bioprocessing methods due to concerns about digitalisation causing potential disruptions. With the lack of expertise and training in operating newly digitalised facilities, companies are hesitant to fully digitalise. Strict regulatory frameworks also pose a significant challenge, as they require thorough validation before adopting new digital systems.
Ensuring data integrity and compliance with these guidelines adds further complexity. For example, companies need to consider Computer software assurance (CSA) and computer systems validation (CSV) when developing new systems for use in drug manufacturing. With machine learning-based systems, new validation approaches are required, further complicating the process.
Standardisation also remains an issue, as different data formats and the interoperability between systems are not well defined. With many of these systems being complex, there are challenges with the integration of digitalisation into existing systems, as many facilities depend on legacy systems that are difficult to align with newer digital solutions. Additionally, costs are also a large barrier in adopting digitalisation, with initial capital expenditure being expensive. Companies need to invest significantly in software, hardware, labour, and training their employees in using the new systems efficiently and correctly, and this can be particularly challenging for smaller companies.
Lastly, while the introduction of cloud-based systems can enhance data management in the bioprocessing industry, they introduce cybersecurity risks and potential data breaches. Companies must carefully consider these while ensuring compliance with global data protection regulations, adding another layer of complexity to adopting digitalisation.
Future of digitalisation
In terms of future outlooks of digitalisation in the bioprocessing industry, it will become increasingly common and points to widespread adoption. At the previously mentioned event, almost 74% of industry stakeholders indicated that digitalisation plays a major role in their current activities. This reflects a strong commitment to embracing Industry 4.0, along with digital tools and processes.
To successfully integrate digital tools into existing bioprocessing systems, there are several key areas to focus on. The first steps involve understanding the data landscape and identifying the processes that would benefit most from digitalisation to unlock value across operations. AI methods and machine learning will play significant roles in automating processes, along with the application of digital twins to create virtual models that enable real time simulations and predictive maintenance. AI-driven control will also enhance efficiency and reduce batch failures.
Companies are expected to move towards fully digital workflows, focusing on end-to-end digitalisation by integrating cloud-based platforms and blockchain technology to enhance traceability and compliance. With standardisation remaining a significant challenge, attempts will be made to complement data formats and integrate distinct digital systems. The adoption of common standards will facilitate seamless data exchange and analysis across the industry. Arguably, the most important aspect of digitalisation in the industry will involve stronger strategic collaborations between manufacturers, suppliers, and regulators. There will be an increasing emphasis on fostering long-term partnerships based on shared data and process insights, driving continuous innovation and efficiency in the bioprocessing industry.

Author
BioFocus Newsroom